Engineering
Product development
InTiCa Systems defines itself as a service and solution provider for its customers and partners. Using the latest methods and technologies, product development embraces both idea generation and market implementation, as well as support throughout the entire product life cycle.
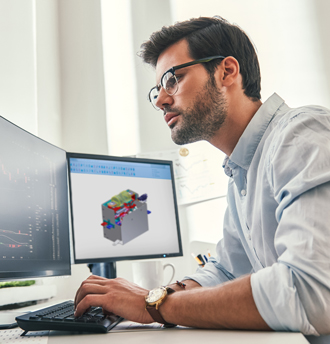
Design
An innovative design is the key to success. State-of-the-art methods guide the product development process from the idea to the final validated product. Market and customer requirements form the basis for a functional and economical design.

Materials
The sustainable use of state-of-the-art materials and the required competence in the choice of materials are our standard. The material know-how at InTiCa Systems covers the areas of plastics as well as copper and ferrite materials and the specific properties of these materials for inductive applications.
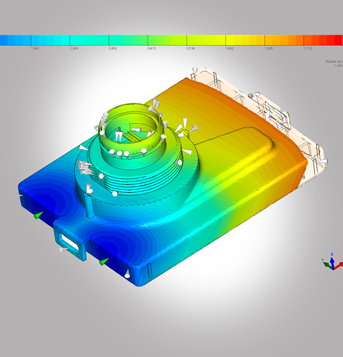
Simulation
Electrical, thermal and mechanical simulation methods enable innovative new product development as well as a continuous optimization of our components in the different product life cycles and development stages. In addition, the simulation of manufacturing processes such as plastic injection molding plays an essential role.
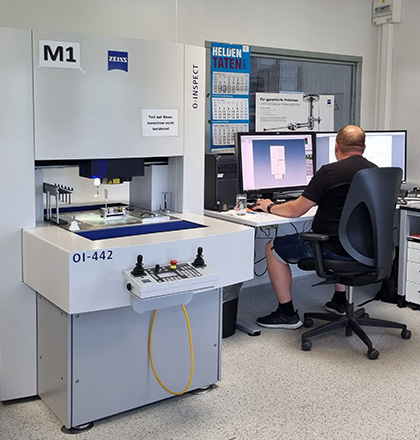
Testing lab
In our electrical and mechanical laboratory, component tests are carried out for a wide range of applications. In particular, the mechanical tactile measurement of components forms the basis of design development and accompanies the complete product development process from the sample phase to series release and beyond to re-qualification.
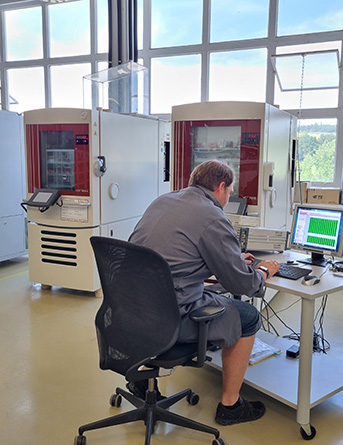
Validation
Extensive product validation processes in line with the respective customer requirements ensure the safety and quality of products and processes during the product life cycle. For this purpose, InTiCa Systems has access to a wide range of equipment at its Technology Center and the premises of partner companies.
Manufacturing technologies
The InTiCa Systems technology portfolio includes injection molding technology with various insert molding and overmolding technologies, outstanding winding processes as well as joining technologies, fully automated product testing and innovative assembly and automation technologies.
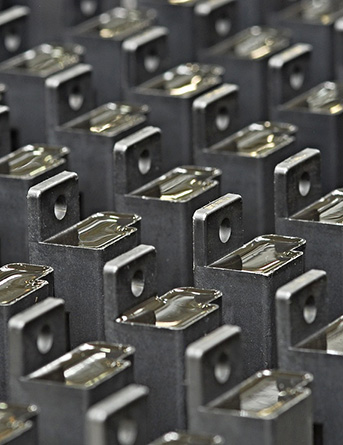
Plastics technology
Plastics technology is one of the core competencies of the InTiCa Systems team. Thanks to our in-depth knowledge of design and processes, we are able to offer a wide range of complex product solutions, especially in the field of overmolding technology with small wall thicknesses. The use of potting technologies, also under vacuum, completes our vast service portfolio.
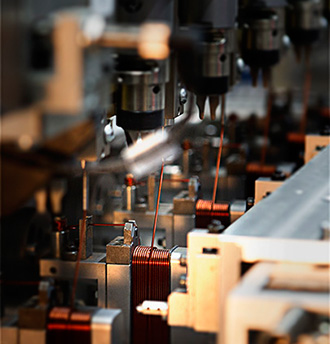
Winding technology
The InTiCa Systems service portfolio in the field of winding technology ranges from manual winding processes to fully automated winding. A wide variety of processes are used for round copper wire, braided wire and flat wire, the latter both horizontally and vertically. InTiCa Systems has also made a reputation for special solutions in winding technology thanks to the know-how of our experts.
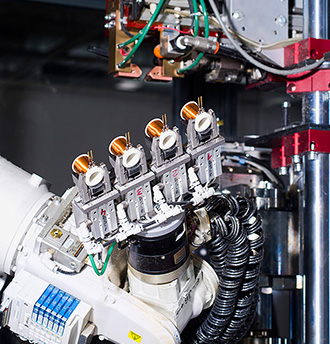
Joining technology
Extensive joining processes for electrical contacting, thermal conductivity, as well as mechanical connection form the foundation of our competence in the area of joining technology. Depending on the application, we employ a wide variety of soldering processes, resistance and laser welding, ultrasonic welding for plastics, adhesive technologies or riveting and screwdriving processes.
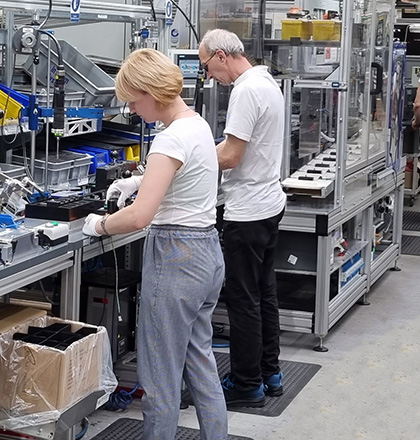
Assembly
Depending on the products, the quantities or the specific processes, a wide variety of assembly processes are used. The manufacturing expertise here includes both very manual and fully automated processes, incorporating the essential process data monitoring. The layout and operational flow of InTiCa Systems' production are based on the principles of lean management.
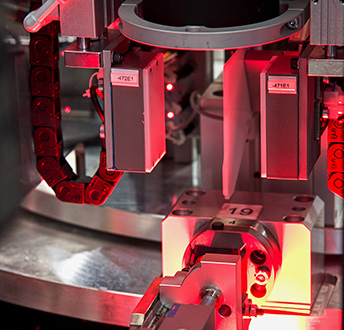
End-of-Line technology
By means of electrical, mechanical, geometric and visual test procedures, we perform 100 percent automated end-of-line testing of our products to ensure complete assembly, flawless function and cleanliness of the components. The monitoring and analysis of the data obtained in the tests is carried out fully automatically.